Copper and Its Water Footprint
Gundega Kalpina
In the sprawling networks of our urban landscapes, two currents flow through hidden modern infrastructures: water and electricity. These parallel streams, tamed and shaped by man, are the lifeblood of our constructed environments. Water, once wild in rivers and streams, now travels through a labyrinth of engineered copper waterways – an underground delta of human design. Carrying its traces of a journey through rock and soil, it emerges chlorinated and pressurized from our taps. Simultaneously, electrons already present in the copper veins are subtly triggered by an electromagnetic field, carrying the energy onward like a cascade of invisible dominoes. This energy, often derived from fossil fuels or nuclear sources, travels vast distances to power our homes and illuminate our spaces. At the heart of both systems lies copper, a reddish-golden metal from the Earth’s crust (Figure 1).
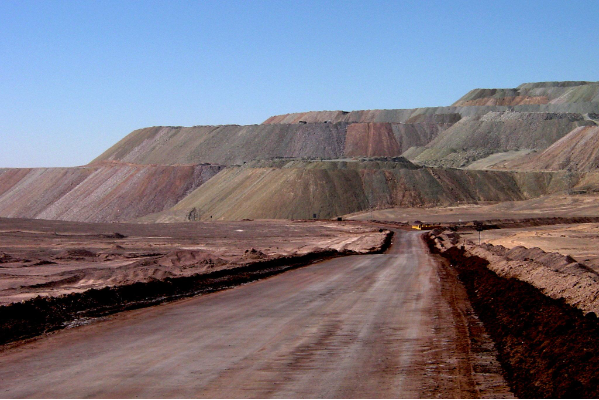
© Bachelot Pierre J-P licensed by: CC BY-SA 3.0
Its unique properties make it the unsung hero of our daily rituals – antimicrobial and durable in water pipes, and highly conductive in electrical wires. These twin flows embody the paradoxes of modernity, representing both the triumph of human technology and our deep entanglement with the geological processes of the natural environment. In the quiet hum of a running computer or a sudden splash of water filling a glass, we hear echoes of transformed landscapes, of dried rivers and mined mountains. Curiously, before electricity runs through copper wires or water rushes through pipes, both elements play pivotal roles in copper’s own extraction and processing. With the transition to renewable energy, the demand for copper products has grown each year, steadily increasing by nearly 60% in the past 18 years [1]. The future looks no different, with demand predicted to double by 2035 [2]. How the global economy’s growing appetite for this essential metal is affecting the earth’s waterscapes and challenging sustainable resource management is revealed in the intertwined paths of water and copper. Gold, silver, copper, and aluminium are integral to the construction industry, particularly in electrical wiring. Buildings rely heavily on these metals, especially copper. However, this is not the first time these materials have come together. High in the mountains of Chile or deep in the soil in Sweden, these precious elements coexist in ores waiting to be mined. Although they don’t really wait – we imagine them to wait. It is our anthropocentric view and our hunger for resources that makes them wait. While copper extraction and production occur in many places, South America stands out, contributing nearly 40% of the world’s annual copper production [3]. Chile, in particular, is exceptionally successful in this endeavour. In 2023 Chile produced 5.3 million metric tons of copper, making it the leading country in copper production [4]. As a result, Chile is the main supplier of copper to Germany and much of Europe. The copper node from Chile is strong, that’s where my quest begins. However, my journey does not start in the physical world. Instead, I travel to the mines along well-trodden paths of knowledge – by reading widely and exploring the mining sites from a bird’s eye view via Google Earth.
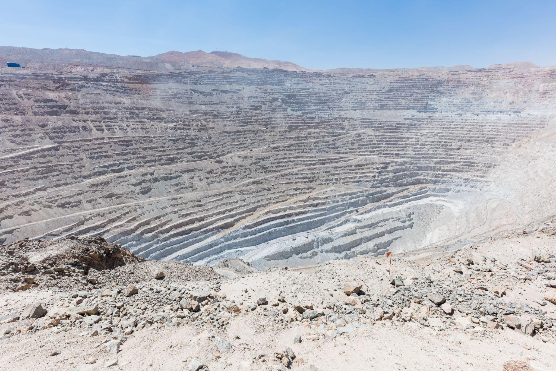
© Diego Delso licensed by: CC BY-SA 4.0
About 135km from the Pacific coast, in the heart of the arid Atacama Desert, the driest place on earth lies Chuquicamata (Figure 2), one of the world’s largest copper mines. From the comfort of my screen, I embarked on a digital exploration of this already centuries-running mine. Tractors the size of two-story houses (Figure 3) navigate hundreds of meters deep mine pits, with paths that change every few days.
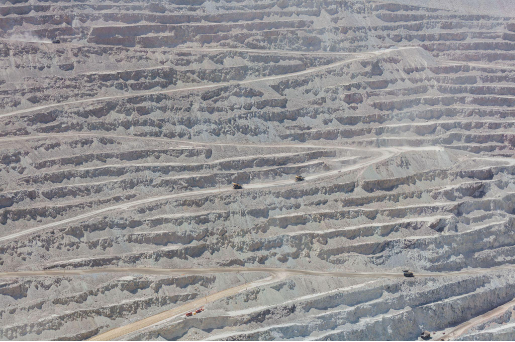
© Diego Delso licensed by: CC BY-SA 4.0
These unique industrial landscapes, sometimes stretching over territories as large as Hamburg Central district (140 km², the mine – 100km²), can be up to 4 km wide and 1000 meters deep. The low concentration of copper in these ores explains the immense size of the mines, which in some cases already exhibit the characteristic red tone of copper (Figure 1). The first step in the process is ore extraction, which involves selecting rocks that contain at least a small amount of copper. For open-pit mining, ores that contain 0.3% copper are considered worth extracting, while for underground mining, the concentration needs to be higher – up to 1.7%. The mines also consist of rocks with no copper inside them – from the industry’s perspective, those are “waste rocks”. A copper mine in Canada produces 30’000 tons of ore and 5 times more the amount of waste rocks [5]. To extract the rock, dynamite is used to blast it into pieces manageable by the tractors. The noise must be deafening, but nobody minds, because the inhabitants of the town closest to the mine were relocated 15 years ago due to health risks [6]. Now only the workers have to endure the strident sounds of the destruction. After the blasting, loading cars work non-stop, 24 hours a day, 7 days a week, transporting between 300 to 600 tons of material on their backs every trip. The massive trucks loaded with copper ore climb from the pit’s depths to the surface, where they unload the ores at a nearby facility. There, a crushing machinery takes in 10,000 tons of rocks every hour, the same weight as the Eiffel Tower. An Eiffel Tower, every hour.
The ore then undergoes a series of grinding stages. By turning and spinning in a mixture of water in a large rotating cylinder, the ore is broken down. It is crushed by steel spheres into pieces as small as grains of sand. The spheres help to crush the rocks more efficiently, ensuring a fine, consistent size for further processing. This marks the initial stage in the process, where water is introduced. Extracting pure copper from ore requires smelting, which involves heating the ore to a temperature beyond the melting point of copper to produce a highly concentrated form of the metal. However, given the low initial concentration of copper in the ores, this process would require an enormous amount of fuel and energy. To increase productivity, the copper minerals are first isolated from the ore by a process called froth flotation. And here water is used again, this time mixed with chemicals which combines with the crushed ore mass in another set of large tanks. Air bubbles are then released from the bottom of the tank and float up through the conglomerate. The valuable metals in the ore such as copper, gold, and silver attach themselves to the air bubbles and float to the surface. This separation method results in a concentrate containing approximately 30% copper, a significant 100-fold increase over the original ore. The remaining rock and unwanted minerals, known as tailings, settle to the bottom of the tank. These tailings, a grey muddy mass, (Figure 4) are later stored in large ponds, slowly evaporating, but staying in place close to the mines.
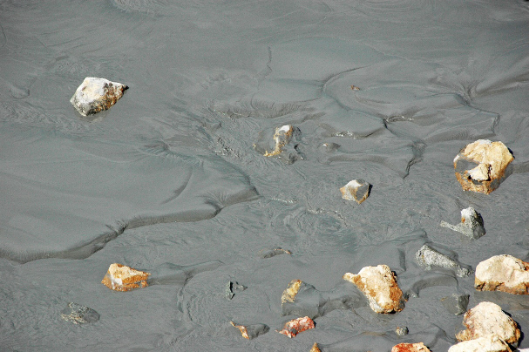
© James St. John licensed by: CC BY 2.0
This practice is concerning because it creates huge reservoirs of toxic waste. Although copper is the material of interest here, high concentrations of it in water can be toxic, as can the other metals such as nickel, chromium or cadmium, that can be found in the tailings ponds. If the water from these ponds leaks out, it can cause serious damage to the surrounding environment and to people if it ends up in rivers or lakes used for drinking water [7]. Some of these tailings ponds are so toxic that guards are employed to scare the birds away, preventing them from landing and drinking the deadly water [8]. This extreme measure underlines the dangerous nature of these waste tailings, which, as copper extraction continues, cover larger and larger areas than the mine itself (Figure 5).
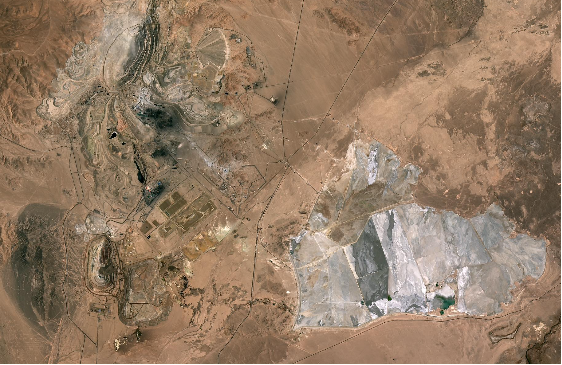
© NASA Earth Observatory, Michala Garrison, using Landsat data from the U.S. Geological Survey, license-free
The remaining copper concentrate is fed into a large smelter, 20 meters long and 7 meters wide. Here, remaining elements like sulfur and iron are oxidized and removed from the concentrate by melting it at a temperature as high as 1250℃, resulting in a copper-rich mass, with more than half consisting of pure copper. The final step involves refining this mass to produce nearly pure copper of 99%, which in many cases happens very far from the mining facilities.
The paths of copper and water intersect significantly throughout the production process, but it is a challenge to determine the exact amount of water involved. To gain insight into this issue, I spoke to a specialist in water footprints. In 2014, a team of researchers including Marcus Berger conducted a comprehensive study, collecting data on the water footprint of the entire copper production process. Berger highlighted that the most significant water use occurs in the early stages of production [9]. Each phase of copper production requires significant amounts of water, although the specific figures vary depending on the mining operation and location. Their study concluded that it takes 53 litres of water to produce one kilogram of copper [10]. This may not sound like much, but when comparing the volumes of these two elements, the mass of water is 530 times larger than the solid block of copper. Considering that 27 million tonnes of copper are produced annually [1], the total amount of water used to produce copper is almost impossible to comprehend. Several approaches are being practiced to reduce water consumption in copper production. However, there is also a way to skip all the most water-intensive steps entirely – recycling. Copper is a 100% recyclable material, which means that all copper that has ever been made in human existence is in circulation now. In Europe, about 43% of consumed copper comes from scrap metal [11], significantly reducing water consumption. Intrigued by this approach, I decided to visit a metal scrapyard to observe first-hand how copper arrives there and what happens afterwards. I was not allowed to enter the scrap yard, but as the site is open to the road, I was able to observe the work from a distance. I witnessed a wide range of copper items being collected. From old wiring and plumbing fixtures to discarded electronic components, the variety of copper sources was impressive (Figure 6).
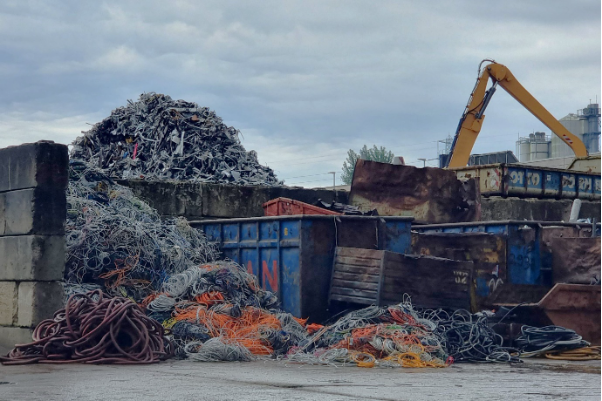
© Gundega Kalpina, licensed under: CC – BY – SA
I watched as workers sorted through piles of metal, expertly identifying and separating copper from other materials. The meticulous sorting process is fascinating to watch, with workers using both manual techniques and sophisticated machinery to ensure that the copper is isolated from other metals and impurities. Conventional mining uses large amounts of water to crush the ore and chemical flotation to separate copper from other minerals. At the scrap yard, however, the water-intensive steps are eliminated and only mechanical sorting methods are used. After sorting, the copper is transported to specialized facilities for remelting and refining. These facilities use advanced techniques to purify the copper, preparing it for reuse in new products. This step, which happens away from the scrapyard itself, is essential for turning scrap copper into high-quality material suitable for manufacturing.
While copper recycling is a great way to conserve water, it is an even more important part of the transition to renewable energy. Electric vehicles, for example, require approximately four times the copper of their conventional counterparts, further intensifying the pressure on copper and water resources [10]. This trend extends to other electrically charged machinery as well. By recycling copper, we reduce the need for new mining, which in turn reduces environmental impact and conserves natural resources. Additionally, recycling copper saves energy and reduces greenhouse gas emissions associated with mining and processing first-grade copper ore and its transportation.
In this context of green energy, copper has also been given a new name – green copper – as it is one of the materials driving this transition. The term “green copper” in the shift to green energy, initially struck me as counter-intuitive. “Green copper” evokes thoughts of history, the image of the distinctively coloured roofs found in historic quarters of European cities. This green hue has often served as a visual guide for me, distinguishing older buildings from more recently renovated ones, and telling the stories of passing times. However, the actual copper with the green patina, which can be seen in cities, is becoming vulnerable to theft. That is the drawback of the recycling process – the price of copper scrap rises, and the easily accessible pieces of copper in reach, like roof sheets of historical buildings, are being stolen. Even railway tracks are being stripped of their wires and then sold as scrap metal. This leads to train delays, for instance in Germany copper wire theft is responsible for a total of 40,000 minutes of delays. That’s not the only downside, there are also safety risks as well as financial losses for the railway companies [12]. At the end these are not just inconveniences, repercussions strongly go against the transition to a more sustainable mobility.
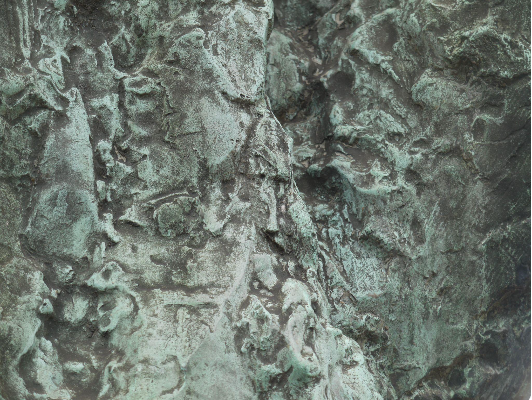
© Gundega Kalpina, licensed under: CC – BY – SA
As the mines were originally designed without water scarcity in mind, and recycling cannot meet the demand for copper, other alternatives are used to reduce water consumption. An increasingly adopted alternative is using seawater instead of fresh water. For instance, at Chuquicamata, this involves transporting water 150km from the coast and nearly 3,000 meters up into the mountains. This is a considerable distance, but measures must be taken to ensure that rivers supplying water to local communities do not dry out. The transport of seawater is very energy-intensive and expensive, and afterwards, the water remains stored in tailings. Another emerging problem is the expiration date of mines. The biggest mine in Chile – Escondida (Figure 1), producing twice as much copper as Chuquicamata is predicted to close in 55 years, for some mines that date is set even sooner, 10 years from now. The Chuquicamata mine is taking steps towards underground mining, but before closing down, in many cases, they start using lower-grade ore, which leads to more ore being needed for the same amount of copper. Consequently, more water must be used to maintain production levels [13]. Water usage in copper extraction will therefore increase, posing challenges for already water-scarce desert and mountain regions where many copper mines are located. The critical question arises: Which will be depleted first – copper reserves or water resources in these mining regions? This highlights the urgent need for sustainable practices in copper production and usage. Once a luxury item, copper is now a key material in making green energy accessible and efficient, reflecting its transformation from a symbol of affluence to an enabler of a sustainable future. It represents the luxury of the old times as well as the luxury of the coming years, in which the electrified world relies on copper. Every drop of water and every gram of copper carries a legacy of environmental consequences. At these crossroads of technological progress and environmental preservation, the actions of today are sculpting the contours of future landscapes, both urban and natural. As inhabitants of this planet, we have the power to determine what these landscapes will reflect of our time – harmony or dissonance between human progress and nature.
[Licensed under: CC – BY – SA]
Sources:
[1] Statista Research Department, Kupfer: Nachfrage Weltweit bis 2023. Statista. https://de.statista.com/statistik/daten/studie/156043/umfrage/weltweite-kupfernachfrage-seit-2006/ accessed on 03.07.2024.
[2] S&P Global Market Intelligence. (2022). The Future of Copper: will the looming supply gap short-circuit the energy transition?
[3] Statista Research Department, Verteilung der Minenproduktion von Kupfer weltweit nach Region im Jahr 2023 https://de.statista.com/statistik/daten/studie/1417145/umfrage/verteilung-minenproduktion-kupfer-weltweit-nach-region/ accessed on 18.07.2024.
[4] Statista Research Department, “Major countries in copper mine production worldwide in 2023”, https://www.statista.com/statistics/264626/copper-production-by-country/ accessed 14.10.2024.
[5] Schlesinger, M. E., Sole, K. C., Davenport, W. G., & Flores, G. R. F. A. (2022). Extractive Metallurgy of Copper. Elsevier. Sixth Edition.
[6] Chile company town goes dust to dust – The Washington Post. (n.d.). https://www.washingtonpost.com/archive/politics/2004/02/01/chile-company-town-goes-dust-to-dust/5abc884e-5143-48ff-8fd0-87a70ad1d6e8/ accessed on 14.10.2024.
[7] Cacciuttolo, C., Cano, D., & Custodio, M. (2023). Socio-environmental risks linked with mine tailings chemical composition: Promoting responsible and safe mine tailings management considering copper and gold mining experiences from Chile and Peru. Toxics, 11(5), 462. https://doi.org/10.3390/toxics11050462.
[8] Al-Arshani, S. (n.d.). This Montana man spends his days shooting at birds that land on a toxic lake to save them from burning inside out. Business Insider. https://www.businessinsider.com/montana-man-shoots-birds-land-toxic-lake-save-them-2023-1 acessed on 13.10.2024.
[9] Berger, M. Interview by Author. Via Zoom on 13.06.2024.
[10] S. Forin, M. Berger, J. Bunsen and M. Finkbeiner, Organizational Water Footprint – Analyzing Water Use and Mitigating Water Scarcity along Global Supply Chains. TU Berlin Chair of Sustainable Engineering, 2021. http://dx.doi.org/10.14279/depositonce-11818.
[11] The International Copper Association. (n.d.-c). Copper recycling. https://internationalcopper.org/wp-content/uploads/2022/02/ICA-RecyclingBrief-202201-A4-R2.pdf accessed 14.10.2024.
[12] Millions of euros and thousands of delays: How copper theft is delaying passengers all over Europe | euronews. (n.d.-b). https://www.euronews.com/travel/2024/02/11/millions-of-euros-and-thousands-of-delays-how-copper-theft-is-delaying-passengers-all-over acessed 14.10.2024.
[13] Plc, G. (n.d.). Chile: Five largest mines in 2021. https://www.globaldata.com/data-insights/mining/chile–five-largest-mines-in-2090624/.